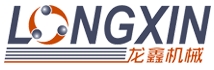
常州市龍鑫智能裝備股份有限公司
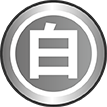
已認證
常州市龍鑫智能裝備股份有限公司
已認證
加氫催化劑市場的蓬勃發展,正推動產業鏈向“高性能、低能耗、綠色化”方向加速轉型。數據顯示,我國加氫催化劑年產量已突破50萬噸,其中干燥環節能耗占比達35%-40%,而粉塵排放與VOCs治理成本年均增長超15%。在“雙碳”目標與新能源材料需求爆發的雙重驅動下,干燥技術的革新已成為催化劑企業降本增效、實現綠色制造的核心突破口。
深入分析加氫催化劑制粒干燥環節,傳統帶式干燥機的技術短板呈多維度顯現:
(1) 物料分布不均導致品質波動:催化劑顆粒(尤其是異形顆粒)在進料時易因攤布器設計缺陷形成“邊緣堆積、中部稀疏”的分布狀態,料層厚度差可達4-6cm,造成干燥后催化劑比表面積差異超過10%,直接影響催化活性的一致性;
(2) 能耗高企與熱效率低下:傳統設備熱風循環依賴單一風機驅動,風壓損失達30%以上,且熱風與物料接觸時間短(平均停留時間<8分鐘),導致干燥能耗高達0.8-1.2kWh/kg水,水平提高40%;
(3) 環保風險與治理壓力:開放式干燥過程中,催化劑粉塵逸散率達5%-8%,部分企業為滿足環保要求不得不額外投入數百萬建設除塵系統,同時干燥尾氣中攜帶的微量有機組分(如造粒助劑揮發物)處理成本居高不下。
某催化劑研究院檢測數據表明,采用傳統干燥工藝的催化劑產品,批次間活性波動幅度達±8%,而環保合規成本占比已超過生產成本的1/5,技術升級迫在眉睫。
龍鑫干燥基于催化劑物料特性(粒徑、堆密度、含水率),打造“精準布風-智能控溫-環保集成”的一體化解決方案:
(1) 均風系統革新:從“無序流動”到“精準穿流”
設備采用“下進上出”穿流干燥工藝,每個干燥單元配備獨立的熱風循環系統,通過機翼型導流板與多孔均風板組合,使熱風在物料層內的風速偏差小。以直徑3mm的球形催化劑為例,熱風穿透速度控制在0.8-1.2m/s,既保證熱交換效率,又避免小顆粒被氣流帶出。對比測試顯示,該系統使熱交換效率提升,較傳統設備節能10%。
(2) 智能分段控溫:動態匹配干燥全周期
基于催化劑干燥“降速干燥-恒速干燥-平衡干燥”三階段特性,龍鑫設備將干燥過程劃分為預熱段(120-140℃)、主干燥段(160-180℃)、均濕段(80-100℃),各段溫度、風量獨立調節。通過PLC智能控制系統,實時監測物料含水率并自動優化運行參數,使干燥時間縮短10-25分鐘,較傳統工藝提升15%效率。
(3) 環保集成方案:從“末端治理”到“源頭控制”
設備采用全密封負壓干燥腔體,配合中效過濾+活性炭吸附的多級尾氣處理系統,粉塵排放濃度<50mg/m3,有機廢氣去除率高。同時,干燥過程中產生的濕熱空氣通過熱泵系統回收能量,用于預熱進料空氣,實現“低排放、低能耗”雙重目標。
在催化劑生產基地,龍鑫帶式干燥機的應用帶來顯著效益:干燥環節人力成本下降60%(全自動化運行),產品批次穩定性提升,年減少粉塵排放。更重要的是,均勻干燥的催化劑在客戶使用中表現出更高的選擇性,為企業帶來產品溢價空間。
隨著加氫催化劑在氫能、煤化工等新興領域的應用拓展,龍鑫干燥以技術創新構建的“環保-效益”雙優模式,正成為行業升級的核心引擎。其方案不僅滿足當前環保合規要求,更通過智能化、節能化設計,為催化劑企業在長期市場競爭中筑牢技術護城河。
最新動態
更多
虛擬號將在 秒后失效
使用微信掃碼撥號